Лазерное притупление острых кромок
Ла́зерное притупле́ние о́стрых кро́мок, технология снятия фаски с кромки хрупкого материала посредством управляемого нагрева лазерным излучением.
Размерная обработка изделий из стекла предполагает, как правило, наряду с операцией резки последующую операцию притупления острых кромок изделий, или снятия фаски. Основное назначение фаски – это обеспечение безопасности при обращении с изделием из стекла и повышение его эксплуатационной надёжности за счёт повышения прочности кромки. Дело в том, что острая режущая кромка стекла сама по себе является концентратором напряжений и представляет собой зону повышенного риска из-за возможного повреждения и разрушения всего изделия при его эксплуатации.
Традиционная технология снятия фаски со стекла базируется на применении алмазно-абразивного инструмента для притупления кромки, шлифования, а зачастую и полирования фаски и всей кромки стекла до получения ровной шлифованной или полированной поверхности. Эта операция весьма трудоёмка и требует значительных дополнительных финансовых затрат. Кроме того, операция снятия фаски сопровождается загрязнением всего изделия из стекла продуктами обработки, что требует дополнительной операции очистки.
Современная технология производства различных типов дисплейных панелей предполагает осуществление всех конечных технологических операций сборки в помещениях в условиях с повышенными требованиями к вакуумной гигиене. Метод лазерного управляемого термораскалывания полностью соответствует этим требованиям, т. к. процесс резки является безотходным и не сопровождается образованием каких-либо посторонних частиц.
Однако возникает необходимость притупления кромок в уже разрезанных в чистых условиях панелях жидкокристаллических экранов LCD или плазменных дисплейных панелях PDP. Это приводит к тому, что изделия подвергают дополнительной операции притупления кромки (или снятия фаски, как обычно принято называть эту технологическую операцию), используя традиционный алмазно-абразивный инструмент.
Недостатком данного способа, помимо низкой производительности, является низкая культура производства и загрязнение изделий продуктами шлифования, а также низкое качество получаемых изделий после алмазно-абразивной обработки кромок, связанное с наличием большого количества микротрещин и нарушенного слоя в зоне обработки. Поэтому в ряде случаев при изготовлении ответственных изделий с повышенными требованиями к прочностным параметрам прибегают к последующей механической или огневой полировке кромок.
Таким образом, в ряде случаев неопровержимые преимущества новой технологии прецизионной безотходной резки – лазерного управляемого термораскалывания (ЛУТ) (Патент № 2024441; Кондратенко. 2015; Кондратенко. 2017; Kondratenko. 2017) – теряются из-за дополнительной операции снятия фасок с помощью алмазно-абразивного инструмента, которая требует проведения последующей операции очистки изделий от продуктов загрязнения.
Разработка нового способа лазерного притупления острых кромок (Патент № 2163226; Патент № 2426700) позволила принципиально решить эту проблему.
Способ притупления острых кромок изделий из стекла с помощью лазерного излучения заключается в следующем. При нагреве острой кромки стекла лазерным пучком с длиной волны излучения 10,6 мкм (рис. 1), для которого стекло непрозрачно, вся энергия поглощается в тонком поверхностном слое.
Рис. 1. Схема нагрева поверхности кромки пластины 1 лазерным пучком 2.Дальнейшее распространение энергии лазерного излучения вглубь материала происходит за счёт теплопроводности. Следовательно, степень нагрева поверхности стекла или другого материала под действием лазерного излучения зависит от следующих факторов: мощности и плотности мощности лазерного излучения, скорости относительного перемещения лазерного пучка и материала, а также скорости отвода тепла от поверхности вглубь материала, которая определяется коэффициентом теплопроводности материала. В результате локального нагрева до температуры, не превышающей температуры плавления, в поверхностных слоях стекла возникают высокие напряжения сжатия, которые компенсируются напряжениями растяжения, расположенными в объёме стекла. В случае выполнения определённых условий нагрева – а именно выбора соответствующей плотности мощности излучения, размеров и формы пучка, а также скорости относительного перемещения изделия и лазерного пучка – можно обеспечить условие, когда напряжения растяжения превысят предел прочности стекла. Это приводит, в свою очередь, к отделению от кромки стекла узкой полоски стекла (рис. 2), за счёт чего и обеспечивается притупление острой кромки пластины, т. е. образование фаски (рис. 3).
При этом притупленная кромка не имеет никаких механических дефектов в виде микротрещин и нарушенного слоя, благодаря чему обладает повышенной механической прочностью.
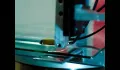
Разработка технологии лазерного снятия фаски со стекла
Для оптимизации технологических режимов процесса лазерного снятия фаски со стекла необходимо установить взаимосвязь между основными параметрами процесса: размерами фаски, скоростью снятия фаски, мощностью лазерного излучения и прочностью кромки стекла. Особое внимание было уделено исследованию повторяемости и стабильности процесса лазерного снятия фаски или определению «технологического коридора», т. е. диапазона обязательных определяющих требований и ограничений, предъявляемых к технологическим параметрам процесса.
Исследования вели с использованием промышленного СО2-лазера мощностью до 100 Вт. На первом этапе были проведены исследования по управлению параметрами, в первую очередь размерами фаски в процессе притупления острых кромок. На рис. 4 приведена зависимость размеров фаски от относительной скорости перемещения лазерного пучка. Исследования осуществляли для трёх значений мощности излучения: 30, 60 и 100 Вт. Ограничение скорости снятия фаски значением 1000 мм/с связано с техническими возможностями используемого оборудования.
Рис. 4. Зависимость размера фаски b от относительной скорости перемещения лазерного пучка v при различной мощности лазерного излучения.Из представленного графика следует, что управление размерами фаски и скоростью притупления кромки находится в очень широком диапазоне. Следует обратить внимание, что для лазерного снятия фаски не требуется большой мощности лазерного излучения. Например, для снятия фаски со скоростью 1 м/с достаточно мощности 100 Вт. Таким образом, по энергетическим затратам технология лазерного снятия фаски является наиболее экономичной из всех ныне существующих технологий. Это делает новую технологию весьма привлекательной для широкого промышленного применения и конкурентоспособной по отношению к традиционным способам притупления острых кромок.
В процессе экспериментальных исследований установлена линейная зависимость скорости снятия фаски от мощности лазерного излучения (рис. 5).
Рис. 5. Влияние мощности лазерного излучения Р на скорость снятия фаски v и её размеры.Из представленных результатов экспериментальных исследований можно сделать вывод, что варьированием скоростью относительного перемещения лазерного пучка и материала, мощностью лазерного излучения и размерами лазерного пучка можно получить фаску заданных размеров в очень широком диапазоне. В ходе проведения исследований были получены размеры фасок от 50 мкм до нескольких миллиметров.
Особое внимание в работе уделено исследованию прочности кромки стекла после лазерного снятия фаски и определению оптимальных технологических режимов процесса, обеспечивающих максимальную прочность изделия. Испытания на поперечный изгиб проводили по установленной методике на универсальной испытательной машине Zwick 1445.
Были проведены сравнительные испытания механической прочности стеклянных пластин толщиной 2 мм при поперечном изгибе после двух различных способов обработки кромок: после механической резки и притупления кромки алмазным инструментом (рис. 6, 1); после лазерной резки и лазерного снятия фаски (рис. 6, 2).
Распределение прочности стеклянных образцов при испытаниях при поперечном изгибе после механического и лазерного притупления кромки приведено на рис. 6. Установлено, что средняя прочность после лазерного притупления кромки стекла в 2,5 раза выше, чем после традиционной обработки кромки.
Рис. 6. Распределение прочности стеклянных образцов при испытаниях при поперечном изгибе после механического притупления кромки 1 и лазерного снятия фаски 2.Кроме увеличения средней прочности кромок после лазерного притупления отмечено заметное увеличение минимального и максимального значений прочности края. Как следует из приведённых данных, максимальные значения прочности после механической обработки соответствуют минимальным значениям прочности кромки после лазерного снятия фаски.
Как показано выше, лазерное притупление кромок стекла может быть осуществлено в широком диапазоне скоростей. Исследовали влияние скорости снятия фаски на прочность кромки. Установлено, что причиной понижения прочности края стекла является появление остаточных термических напряжений при чрезмерном снижении скорости снятия фаски без одновременного уменьшения мощности лазерного излучения, что приводит к перегреву стекла до появления пластических деформаций.
Результаты зависимости прочности края стекла от скорости снятия фаски при постоянной мощности лазерного излучения 100 Вт приведены на рис. 7.
Рис. 7. Зависимость прочности стеклянной пластины от скорости снятия фаски v при постоянной мощности лазерного излучения 100 Вт. Увеличение скорости снятия фаски с 300 до 1000 мм/с приводит к двукратному увеличению прочности края стекла – с 80 до 160 МПа. Логично, исходя из представленных данных, выбирать оптимальное значение скорости снятия фаски в диапазоне 800–900 мм/с по следующим соображениям. Данное значение скорости обеспечивает практически максимальную прочность кромки при высокой производительности и 100%-ной повторяемости и надёжности процесса лазерного снятия фаски.
При необходимости увеличения размера фаски следует прибегать к уменьшению скорости с одновременным уменьшением мощности лазерного излучения в целях уменьшения плотности мощности лазерного излучения в зоне нагрева кромки. Увеличение производительности процесса лазерного снятия фасок больших размеров обеспечивается увеличением длины эллиптического пучка с одновременным увеличением мощности лазерного излучения.
Технологию лазерного снятия фаски следует рассматривать как одну из разновидностей метода ЛУТ хрупких неметаллических материалов со всеми присущими этому методу особенностями и возможностями. Это означает, что снятие фаски можно осуществлять не только на стекле, но и на таких материалах, как сапфир, кварц, керамика, полупроводниковые материалы.
В ходе выполнения исследований совместно с тайваньской компанией Foxconn Technology Group Ltd. было разработано специализированное технологическое оборудование для резки и притупления острых кромок изделий из стекла и сапфира при производстве дисплейных панелей и смартфонов. Данное оборудование позволяет осуществлять в автоматическом режиме прецизионную вырезку изделия из заготовки, отделение облоя и снятие фаски с обеих сторон.
Следует отдельно подчеркнуть, что технология лазерного снятия фаски может эффективно использоваться не только в сочетании с прецизионной резкой методом ЛУТ, но и при снятии фасок со стекла после традиционной механической резки алмазными или твердосплавными резцами. При этом благодаря удалению повреждённой при резке дефектной кромки стекла технология позволяет получать изделия с очень высокой механической прочностью, близкой к прочности края после лазерной резки и снятия фаски.
Выводы
Полученные в ходе исследований результаты позволяют сделать вывод о бесспорном преимуществе разработанной технологии лазерного снятия фасок со стекла и других хрупких неметаллических материалов и о перспективности применения этой технологии в различных областях производства.
Основные преимущества технологии лазерного снятия фасок со стекла и других хрупких неметаллических материалов перед известными традиционными технологиями:
многократное повышение производительности процесса снятия фаски со скоростью до 1 м/с;
повышение прочности изделия в 2 раза и более за счёт бездефектности кромки и отсутствия остаточных напряжений;
отсутствие загрязнения изделия продуктами обработки, что позволяет использовать технологию в условиях с повышенными требованиями к чистоте, в т. н. чистых комнатах;
низкие энергетические затраты;
высокое качество фаски, не требующее дополнительной полировки;
отсутствие продуктов загрязнения поверхности изделий в процессе снятия фаски, что позволяет осуществлять операцию снятия фасок в условиях повышенной чистоты и вакуумной гигиены;
отсутствие продуктов утилизации и полная экологическая чистота процесса снятия фасок;
отсутствие дополнительных расходных материалов;
полная автоматизация процесса резки и снятия фасок при изготовлении изделий свободной формы;
резкое сокращение расходов, повышение производительности и снижение себестоимости процесса снятия фасок после традиционной механической резки.