Лазерное управляемое термораскалывание
Ла́зерное управля́емое те́рмораска́лывание (ЛУТ), технология размерной резки хрупких неметаллических материалов под действием термоупругих напряжений, возникающих в результате нагрева линии реза лазерным излучением с последующим охлаждением зоны нагрева хладагентом. При облучении поверхности хрупкого материала лазерным излучением с длиной волны, для которой материал является непрозрачным, часть энергии отражается от границы воздух – материал, а остальная часть поглощается и выделяется в виде тепловой энергии в приповерхностном слое материала. При облучении поверхности непрозрачного хрупкого материала лазерным излучением во внешних его слоях возникают значительные напряжения сжатия, которые, однако, к разрушению не приводят. При выходе нагретого участка из зоны воздействия лазерного излучения начинается охлаждение поверхностных слоёв материала. При подаче хладагента вслед за лазерным пучком происходит резкое локальное охлаждение поверхности материала по линии реза. Создаваемый градиент температур обусловливает возникновение в поверхностных слоях материала напряжений растяжения, превышающих предел прочности материала, которые приводят к образованию микротрещины, проникающей вглубь материала на глубину до внутренних прогретых слоев, испытывающих напряжения сжатия. Таким образом, в материале на границе зон нагрева и охлаждения, т. е. в месте максимального градиента температур «нагрев – охлаждение», образуется микротрещина, глубина которой определяется распределением термоупругих напряжений, зависящим от целого ряда факторов.
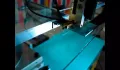
История метода ЛУТ
Первые работы, посвященные описанию новой технологии размерной резки методом ЛУТ, появились в конце 1970-х гг. (авторское свидетельство СССР № 708 686, приоритет от 17.8.1977) и имели ограничения к широкому доступу. В 1990 г. работа по созданию и внедрению высокоэффективного процесса обработки стекла на основе новых способов лазерной резки, а именно метода ЛУТ, была удостоена премии Совета Министров СССР в области науки и техники. Открытое патентование метода ЛУТ в 1992 г. в России (патент РФ № 2 024 441, приоритет от 2.4.1992) и за рубежом (Международная заявка WO9 320 015, приоритет 14.10.1993) российским исследователем, профессором В. С. Кондратенко, можно считать началом широкого развития и международного внедрения ЛУТ.
Доля использования таких хрупких материалов, как стекло, сапфир, керамика, кварц, полупроводниковые материалы, в том числе кремний, резко возрастает практически во всех отраслях производства. Также резко растет номенклатура изделий, использующих указанные выше материалы. К ним относятся изделия остекления транспортных средств, стеклянные изделия архитектурного применения (строительное стекло), подложки твердотельных полупроводниковых приборов, изделия оптики и оптоэлектроники. Существующие традиционные технологии и оборудование обработки перечисленных хрупких неметаллических материалов практически исчерпали свои возможности и требуют качественного изменения.
Традиционные технологических процессы обработки указанных материалов характеризуются большим количеством трудоёмких ручных операций, низким процентом выхода годных изделий. Обработка прецизионных изделий из хрупких неметаллических материалов основана на операциях резки твердосплавным или алмазным инструментом, шлифования и доводки кромок алмазно-абразивным инструментом, а в ряде случаев механического или огневого полирования кромок.
В этих условиях актуальна задача поиска и разработки новых эффективных методов обработки хрупких материалов, которые должны удовлетворять постоянно растущим требованиям к качеству, конструкционным и эксплуатационным параметрам прецизионных изделий из стекла и других хрупких неметаллических материалов, а также обеспечивать массовость и всевозрастающую номенклатуру их выпуска.
За работу «Разработка и промышленное внедрение новых высокоэффективных технологий и оборудования для обработки стекла и других хрупких неметаллических материалов» коллективу под руководством В. С. Кондратенко была присуждена премия Правительства РФ в области науки и техники 2005 г. В 2014 г. Всемирная организация интеллектуальной собственности (World Intellectual Property Organization) наградила автора метода ЛУТ В. С. Кондратенко золотой медалью и дипломом лауреата премии «Лучший изобретатель», а в 2018 г. Международная федерация изобретательских ассоциаций (International Federation of Inventors Associations) – золотой медалью «За лучшее изобретение».
Базовая технологическая схема метода ЛУТ
Схема образования микротрещины при ЛУТ приведена на рис. 1. При нагреве лазерным эллиптическим пучком 1, фокусируемым с помощью сферическо-цилиндрического объектива 3, поверхности хрупкого материала 2, непрозрачного для используемой длины волны лазерного излучения, в зоне нагрева в поверхностных слоях возникают напряжения сжатия Qсжат.. При подаче с помощью форсунки 4 хладагента 5 (воздушно-водяной аэрозоли) вслед за лазерным пучком происходит резкое локальное охлаждение поверхности материала по линии реза. Создаваемый градиент температур обусловливает возникновение в поверхностных слоях материала напряжений растяжения Qрас., превышающих при определенных условиях предел прочности материала, что приводит к образованию микротрещины 6.
Рис. 1. Схема процесса ЛУТ.Несмотря на кажущуюся простоту физической модели метода ЛУТ, для управления технологическими параметрами процесса ЛУТ необходимо учитывать взаимосвязь между большим количеством влияющих друг на друга факторов. Первостепенное значение для процесса ЛУТ имеют 5 факторов.
1. Свойства и характеристики раскалываемого материала:
механические – хрупкость, прочность, состояние поверхности (шероховатость и поверхностные напряжения);
теплофизические – коэффициент линейного термического расширения, температура плавления, теплоёмкость, температуропроводность, термостойкость;
оптические – коэффициенты поглощения, пропускания и отражения.
2. Параметры лазерного излучения:
модовая структура;
импульсно-периодические свойства;
мощность и плотность мощности;
форма и размеры пучка излучения на поверхности материала.
3. Параметры хладагента:
теплофизические свойства, в том числе теплоёмкость, удельная теплота парообразования, температура кипения;
количество хладагента и интенсивность его подачи;
форма и размеры потока хладагента на поверхности материала.
4. Применяемое дополнительное воздействие на раскалываемый материал:
создание первичного концентратора напряжений;
тепловое воздействие на материал (нагрев, охлаждение);
воздействие акустических волн.
5. Скорость относительного перемещения раскалываемого материала и лазерного пучка с хладагентом.
Для оптимизации режимов ЛУТ для различных материалов необходимо установить и исследовать взаимосвязь между указанными выше основными параметрами, характеризующими этот процесс.
Критерии и условия для реализации метода ЛУТ
На основании многочисленных теоретических и экспериментальных исследований и с учетом многолетнего практического опыта сформулированы основные критерии и условия для реализации метода ЛУТ для различных хрупких неметаллических материалов.
1. Нагрев разделяемого материала лазерным излучением должен быть поверхностным.
Другими словами, для каждого типа материала исходя из его оптических свойств следует выбирать длину волны лазерного излучения, для которой материал непрозрачен и излучение должно поглощаться в тонком поверхностном слое материала. Например, для стекла, основных типов керамики, сапфира и кварца – это излучение СО2-лазера с длиной волны излучения 10,6 мкм, которое поглощается в перечисленных материалах в тонком поверхностном слое порядка длины волны излучения. Для резки методом ЛУТ таких полупроводниковых материалов, как кремний и арсенид галлия, используется излучение полупроводникового лазера с длиной волны 808 нм.
2. Максимальная температура нагрева поверхности разделяемого материала не должна превышать температуры его плавления или размягчения.
Это означает, что при нагреве поверхности материала возникающие термоупругие напряжения не должны превысить границу пластичных деформаций.
3. Должен иметься или искусственно создаваться служащий началом развития разделяющей трещины первоначальный концентратор напряжений в виде короткой царапины или иного дефекта на поверхности либо на некоторой глубине материала по линии разделения.
4. Должен быть создан локальный градиент температур, обеспечивающий появление напряжений растяжения, превышающих предел прочности материала, и образование разделяющей микротрещины; для этого на поверхность материала в зону нагрева вслед за лазерным пучком подаётся хладагент.
Перечисленные четыре основных критерия обязательны для обеспечения условий образования разделяющей микротрещины, т. е. для реализации процесса ЛУТ.
При соответствующем соотношении между указанными выше параметрами процесса разработаны следующие разновидности процесса ЛУТ:
получение микротрещины, проникающей на заданную глубину под заданным углом к поверхности материала, в том числе получение сквозной трещины;
лазерное параллельное термораскалывание, т. е. образование трещины в объёме материала на заданной глубине, распространяющейся параллельно поверхности материала, без повреждения самой поверхности материала;
одновременное образование двух взаимно перпендикулярных трещин: перпендикулярной и параллельной поверхности материала;
образование канавок на поверхности материала заданной глубины и ширины на заданном расстоянии друг от друга;
лазерное притупление острых кромок изделий не за счёт оплавления, а за счёт отделения части материала под действием термоупругих напряжений.
Метод ЛУТ применим для резки следующих хрупких неметаллических материалов:
любые типы стекла, включая кварцевое стекло;
сапфир;
любые типы керамики;
полупроводниковые материалы: кремний, арсенид галлия и др.
На рис. 2 приведены сравнительные результаты резки одинаковых образцов стекла толщиной 0,4 мм по линиям реза свободной формы методом ЛУТ (рис. 2а) и резки с помощью пикосекундного лазера (рис. 2б). Метод ЛУТ продемонстрировал пятикратное преимущество по скорости резки (350 мм/с против 70 мм/с) и значительное повышение качества кромки стекла, а именно: уменьшение шероховатости поверхности в 240 раз (с Ra = 1,2 мкм при резке пикосекундным лазером до Ra = 0,005 мкм при резке методом ЛУТ). Также следует отметить, что ширина реза методом ЛУТ равна нулю, в то время как при резке пикосекундным лазером ширина реза составляет 120 мкм.
Рис. 2. Сравнительные результаты резки стекла толщиной 4 мм методом ЛУТ и пикосекундным лазером.
Характеристики метода ЛУТ
Технические характеристики:
скорость резки – до 1 м/с;
толщина материала – от 0,03 до 30 мм;
ширина реза равна нулю;
минимальный размер заготовки – 0,03 мм;
максимальный размер отрезаемой заготовки – не ограничен;
мощность лазерного излучения – 10–200 Вт.
Технологические характеристики:
безотходность процесса разделения материала;
высокая чистота процесса, не загрязняющего поверхность материала при резке;
нулевая ширина реза;
высокая скорость резки, достигающая 2 тыс. мм/с;
высокая точность раскроя материалов;
высокое качество кромки изделия после резки, сравнимое с оптически полированной поверхностью, – невидимость линии состыковки торцов отдельных элементов в единое изделие;
отсутствие механических нагрузок на заготовку в процессе реза методом ЛУТ – снижение ограничений на толщину заготовки после её утонения;
отсутствие снижения прочности кромки изделия (при механической резке прочность детали снижается в 2,5–5 раз).
Применение метода ЛУТ
Широкое распространение и эффективное применение метода ЛУТ обеспечивает математическая модель, описывающая процесс развития трещины в хрупком материале под действием знакопеременных термоупругих напряжений, создаваемых лазерным излучением и хладагентом. Разработанная теория метода ЛУТ эффективно используется не только для изотропных, но и для анизотропных материалов, а также разработаны и оптимизированы различные технологии прецизионной обработки материалов.
Среди перспективных направлений развития технологий, базирующихся на применении метода ЛУТ, следует выделить резку следующих материалов и изделий:
плоских дисплейных панелей (ПДП);
сенсорных и защитных экранов для смартфонов и других изделий;
стекла в процессе выработки;
изделий остекления транспортных средств;
стеклоизделий архитектурного назначения;
монокристаллического кварца и стекла для оптических фильтров;
приборных пластин из сапфира на кристаллы;
различных типов керамики;
кремния и других полупроводниковых материалов;
стеклянных труб.
В. С. Кондратенко сформулирована общая концепция конструирования лазерного технологического оборудования для прецизионного разделения различных материалов методом ЛУТ. Концепция конструирования позволила разработать и организовать серийный выпуск высокоэффективного оборудования для реализации метода ЛУТ. В 2022 г. в мире насчитывалось более тысячи единиц специализированного технологического оборудования, использующего метод ЛУТ.
Особенности резки методом ЛУТ в перпендикулярных направлениях
Первые попытки использования метода ЛУТ для резки приборных сапфировых пластин на кристаллы в производстве светоизлучающих диодов показали его перспективность и бесспорные преимущества.
Главным преимуществом технологии ЛУТ является высокая производительность (скорость резки 700–1,5 тыс. мм/с) и бездефектность кромки, что препятствует снижению прочности изделия в 5 раз по сравнению с традиционной резкой.
Однако при попытках применения метода ЛУТ в массовом производстве светоизлучающих диодов (СИД) возникли некоторые трудности, преодоление которых потребовало дополнительных исследований.
Несмотря на все преимущества метода ЛУТ, возникают определенные трудности при резке методом ЛУТ по пересекающимся линиям. Высокопрочная бездефектная кромка пластины после ЛУТ препятствует продвижению трещины при пересечении первоначальных линий реза в перпендикулярном направлении.
Резка сапфировых или других приборных пластин в первом направлении осуществляется без всяких затруднений со скоростью от 350 до 700 мм/с, при этом используется излучение СО2-лазера мощностью 25–50 Вт.
Рис. 3. Фотография кристалла светодиода и торцов кристалла СИД после резки методом ЛУТ.На рис. 3 показана фотография кристалла СИД размером 350×350 мкм2 после резки исходной сапфировой пластины методом ЛУТ: стороны 1, 2 – после резки в первом направлении; стороны 3, 4 – после резки во втором направлении.
Как видно на этой фотографии, резку в первом направлении отличает высокое качество кромки, в то время как резка во втором направлении происходит с заметным искривлением линии реза. Несмотря на нанесение надреза во втором направлении с помощью алмазного резца, происходит отклонение линии реза от прямолинейной траектории перемещения. Кроме того, качество торца кристалла во втором направлении резки существенно хуже качества резки в первом направлении. Ещё одним недостатком такого способа резки является быстрый износ алмазного инструмента для нанесения надреза.
В ходе выполнения исследовательских работ по оптимизации технологического процесса лазерной резки приборных пластин, в первую очередь на основе сапфировых подложек, был разработан и запатентован новый способ резки (Патент РФ № 2 404 931, приоритет от 28.8.2009).
На рис. 4 представлена схема лазерной резки приборных пластин на кристаллы, сочетающей метод ЛУТ и нанесение неглубокого надреза во втором направлении с помощью ультрафиолетового лазера.
Рис. 4. Схема лазерной резки приборных пластин на кристаллы методом ЛУТ.Резку сапфировой пластины 1 со сформированными структурами 2 осуществляют следующим образом:
При резке пластины в первом направлении первоначально на краю пластины наносят короткие надрезы 3, являющимися концентраторами напряжений и обеспечивающими надёжное зарождение и продвижение разделяющих трещин 4 методом ЛУТ.
При резке во втором направлении для получения сквозных разделяющих трещин 5 предварительно наносится неглубокий надрез 6 по всей длине реза или в местах пересечений с линиями реза 4 с помощью сфокусированного пучка УФ-лазера 7.
При последующем нагреве линии надреза 6 лазерным пучком 8 СО2-лазера и последующем охлаждении зоны нагрева с помощью хладагента 9 происходит образование сквозной разделяющей трещины 5.
Была осуществлена оптимизация технологических режимов резки приборных пластин со структурами светоизлучающих диодов на кристаллы. В качестве материала использовалась пластина из сапфира диаметром 50,8 мм, толщиной 90 мкм. Резку подложки на кристаллы (чипы) размерами 250×250 мкм2 осуществляли на лазерной технологической установке, содержащей СО2-лазер мощностью до 50 Вт, обеспечивающий генерацию излучения с модой ТЕМ01, имеющей два распределённых в пространстве пика излучения. Излучение фокусировалось на поверхность пластины с помощью сферическо-цилиндрического объектива в эллиптический пучок размером 1,5×0,1 мм². Рис. 5. Кристалл СИД после резки сапфировой пластины методом ЛУТ с применением надреза УФ-лазером.Для нанесения локальных надрезов длиной 150 мкм на краю пластины при резке в первом направлении и нанесения надрезов по всей длине реза во втором направлении использовали УФ-лазер с длиной волны излучения 355 нм. Глубина надреза составляла 5–9 мкм, а ширина – 5–7 мкм. Скорость резки пластины методом ЛУТ составила 400–550 мм/с.
На рис. 5 показана фотография кристалла СИД после резки сапфировой пластины методом ЛУТ по новой технологии, обеспечивающей высокое качество резки в первом и втором направлениях.
Первая отечественная промышленная установка резки сапфировых пластин на кристаллы была сделана в г. Зеленоград.