Мукомольное производство
Мукомо́льное произво́дство, производственный процесс по переработке зерна в муку, осуществляемый на мукомольном заводе (мукомольной мельнице). История возникновения и развития мукомольного производства насчитывает несколько тысячелетий. Основа современной технологии размола зерна была заложена в конце 19 в. с созданием вальцового станка, просеивающей машины (рассева), ситовеечной машины. Современная мукомольная мельница представляет собой практически полностью автоматизированное поточное производство. В зависимости от вида помола, сельскохозяйственной культуры (пшеницы, ржи, гречихи и др.) и производительности мукомольные заводы существенно различаются по техническому оснащению. Так, мукомольный завод, перерабатывающий до 50 т зерна в сутки (т. н. мини-мельница) с минимальным набором оборудования, может включать 4–12 вальцовых систем и размещаться в одноэтажном здании; мукомольный завод производительностью 500–1000 (и более) т зерна в сутки – 12–20 вальцовых и 4–8 ситовеечных систем и занимать здание в 6–8 этажей. Наиболее сложное производство – помол твёрдой пшеницы в макаронную муку (только ситовеечных систем может быть 40 и более).
Выгрузка пшеницы на мукомольном заводе.
Элеваторы при мукомольных заводах позволяют хранить достаточно большие объёмы зерна, что обеспечивает формирование стабильных по качеству помольных смесей из зерна с различными свойствами, необходимых для длительной работы завода без переналадки оборудования. Технология размола зерна различных культур не имеет принципиальных различий; наиболее распространён помол пшеницы мягких сортов в сортовую хлебопекарную муку. Подготовка зерна к помолу производится в зерноочистительном отделении, где осуществляют очистку от различных примесей и дефектного зерна, шелушение (очистку поверхности зерна) «сухим» или «влажным» (мойка зерна или мокрое шелушение) способом, раздельное (в несколько параллельных потоков) кондиционирование зерна с различными свойствами. Зерно отдельных потоков объединяют для окончательной очистки от примесей и частичного удаления оболочек. Непосредственно перед измельчением зерновую смесь увлажняют на 0,2–0,5 % с кратковременной выдержкой (отволаживанием).
Подготовленное зерно поступает в размольное отделение. Размол зерна в вальцовых станках с последующей сортировкой продуктов размола в рассевах проводят поэтапно. Первоначально производят измельчение (т. н. драной процесс) таким образом, чтобы получить 60–65 % промежуточных продуктов (т. н. крупки и более мелкий – дунст) и 15–20 % муки. Крупки и дунст поступают на ситовеечные машины, где их разделяют на фракции по добротности (содержанию эндосперма). Фракции, состоящие только из эндосперма, направляют на размольные системы (8–12 систем для измельчения промежуточных продуктов в муку). Фракции из сростков, содержащие преимущественно эндосперм и незначительное количество оболочек, – на шлифовочные системы. Фракции, включающие значительное количество оболочек, поступают на системы вымола (последние системы драного и размольного процессов). На ситовеечных машинах получают также манную крупу. На системах шлифовочного процесса производят измельчение таким образом, чтобы избежать дробления оболочечных частичек; получаемые при этом крупки и дунст направляют на размол, сходовые (с сита) продукты – на системы вымола, муку – на контроль. Отруби получают на последних системах драного и размольного процессов.
Мука, поступающая с разных систем, отличается по качеству (в зависимости от положения системы в общей структуре размола). С начала 21 в. формирование сортов муки, как правило, производят в специальном отделении завода (цех формирования сортов муки), где осуществляются размещение муки различных видов и сортов в отдельные ёмкости, подготовка предсмесей (т. н. премиксов, состоящих из витаминных, ферментных препаратов и др.), последующее дозирование и смешивание компонентов для получения муки и мучных смесей с заданным химическим составом и реологическими свойствами. Полученную муку в выбойном отделении мукомольного завода фасуют, например, в мешки, пакеты (до 2 кг) или загружают в автомуковозы (бестарный способ).
Мукомольное производство включает десятки километров транспортных коммуникаций, состоящих из самотёчных и пневматических трубопроводов, винтовых и цепных конвейеров, норий. Технологический процесс производства муки характеризуется высоким потреблением электроэнергии (на производство 1 т муки расходуется от 20 до 120 кВт в зависимости от вида помола и внутрицехового оборудования) и воздуха (до 10 т на производство 1 т муки). Мукомольное производство относится к взрывопожароопасному производству, поэтому на мукомольных заводах применяются эффективные технические средства взрыво- и противопожарной защиты; например, устанавливаются магнитные сепараторы для улавливания металломагнитных примесей (магнитная защита) перед измельчающими машинами, взрыворазрядители на потенциально опасном оборудовании, автоматизированные системы противопожарной защиты, осуществляется аспирация (т. е. отсасывание воздуха от места образования пыли). Также нормируется содержание пыли по SiO2.
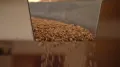